Safe Work Procedures
Do you have them in your workplace?
What is a Safe Work Procedure?
A Safe Work Procedure (SWP) or Standard Operating Procedure (SOP) documents the risks associated with a work task, and lists the appropriate risk control measures into a sequence of steps for performing the task or activity safely. SWP’s are most effective when developed in consultation with your workers.
SWP’s / SOP’s provide information to assist your workers to perform tasks safely. These procedures can also assist in the training and orientation of new workers in the hazards of the task being performed, as well as providing your workers with the preferred way to safely perform the task/activity. They are also a useful tool when training and supervising your workers, and when responding to incident reports and changes in the workplace.
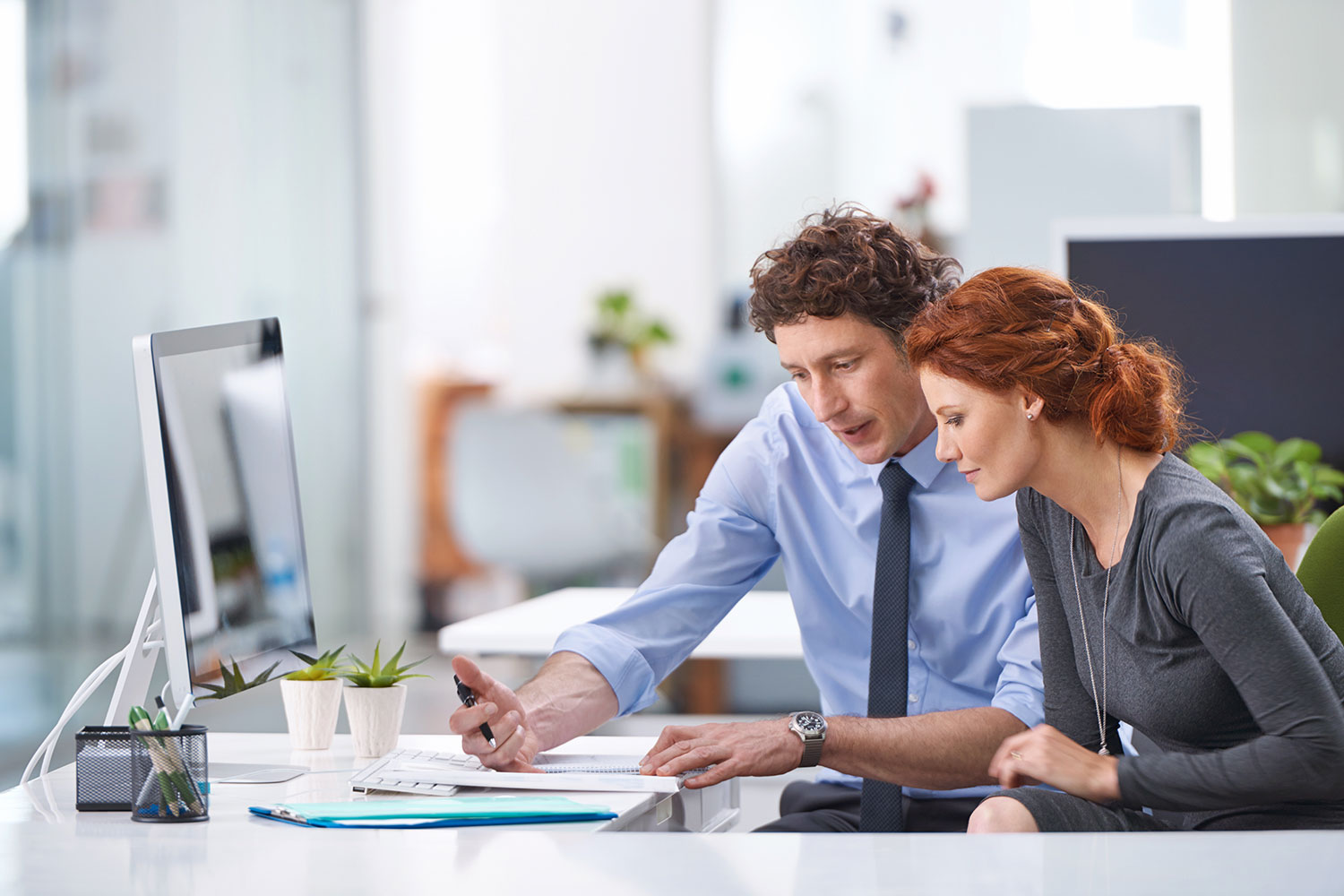
What is your obligation in relation to Safety Procedures in your workplace?
Persons Conducting a Business or Undertaking (PCBU’s) are required by law to provide and maintain safe working environments and safe systems of work for all persons who enter the workplace.
When should you develop a Safe Work Procedure?
SWP’s / SOP’s are required to be created for key work processes in your workplace that involve risk to your workers. For example, when new equipment or new chemical has been introduced to the workplace, or when existing procedures or processes are changed.
Who do Safe Work Procedures apply to?
All workers including contractors and volunteers must be inducted, and given regular training in relevant SWP’s / SOP’s that apply to the work task/activity to be performed. PCBU’s must also ensure that they have evidence all workers are competent to perform these procedures.
How do you prepare a Safe Work Procedure?
When preparing a Safe Work Procedure:
- Identify the tasks and activities in your workplace that require a SWP / SOP. The tasks and activities can be identified through consultation with workers, knowledge and observation of the job requirement/s.
- Perform a risk assessment to identify the most critical tasks/activities that have the highest level of risk, this will assist in determining the order of priority in developing SWP’s / SOP’s for your business activities.
- Review the most critical tasks/activities to determine what hazards are associated with the task/activity. When describing a hazard, ensure the hazard is identified – for example What injury or illness might occur as a result of the hazard? How may the hazard occur and who it may happen to?
- Determine how to complete the job safely. After each hazard has been identified determine if there is another practical way to eliminate the risk, if this is not possible use the hierarchy of controls.
- Review the document. Once the SWP / SOP has been completed, issue a draft copy to all your workers for consultation and review. This will ensure there are no gaps and the content of the document is accurate. All workers need to approve the final draft.
- Approve and issue the SWP/SOP for use. Ensure a hard copy is kept in a suitable place for reference and displayed in the work area where the procedure or task is performed.
What about the Training and Competency of Workers?
All workers performing a task in your workplace must be instructed, trained and educated on the hazards of the task and how to follow the SWP / SOP. Instruction, education and training is required, and must be tested to ensure the training has been effective. Under the WHS Act – the PCBU must also be sure that workers are competent in performing the task / activity and retain records of the competency.
When should you review your Safe Work Procedure?
SWP’s / SOP’s are required to reviewed typically every one (1) to two (2) years or at the frequency specified on the approved document. Other considerations for review can include:
- If you are requested by a worker or contractor.
- If there are repeated non-compliance’s with the documented SWP / SOP.
- If there is a change to a task, process or equipment in the workplace.
- If there has been an incident involving the task/activity, this includes whether the incident resulted in an injury or a near miss.
- If there is updated information about a hazard this information may be from an internal or external party i.e. from a worker or safety regulator.
Conclusion
If you’re looking for assistance with WHS/OH&S requirements specific to your industry, please contact WHS Consulting Hunter for advice on how to incorporate safety management into your business operations.
WHS Consulting Services
For expert assistance in implementing effective WHS training and programs, small business owners in Hunter, Newcastle, Central Coast, Mid North Coast, and Sydney can turn to WHS Consulting Hunter. Our team of experts is dedicated to helping businesses create safer workplaces while adhering to Australian WHS standards and codes of practice.
0419 847 771
jason@whsch.com.au